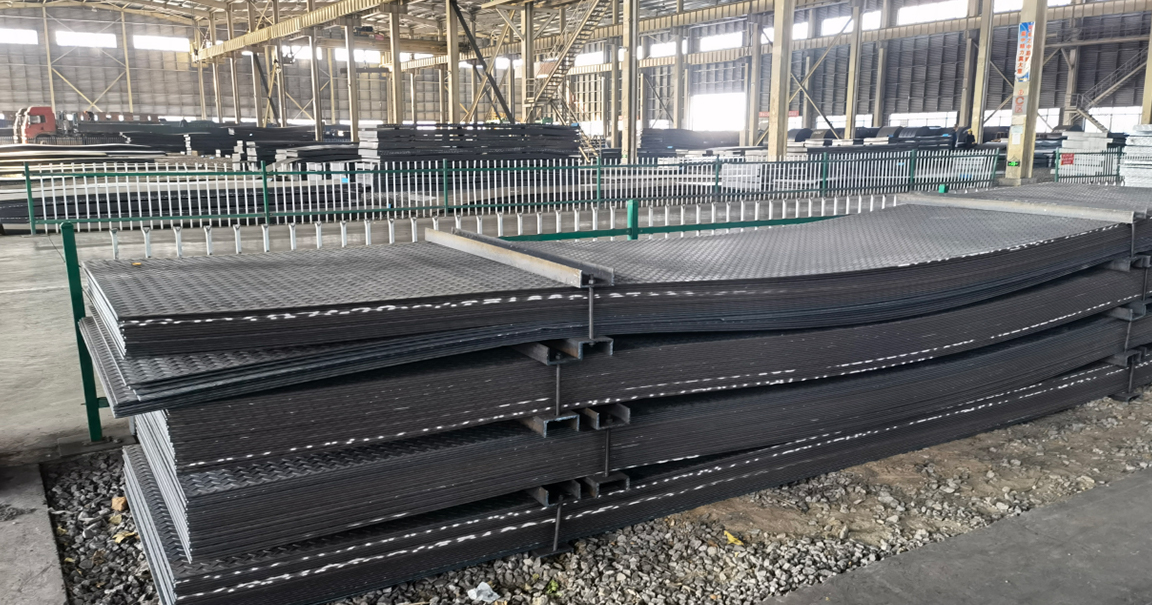
The performance characteristics of high carbon steel plates and sheets are largely determined by their heat treatment processes, which transform the material's microstructure to achieve desired mechanical properties. These carefully controlled thermal processes represent a critical phase in manufacturing, where the steel's hardness, toughness, and wear resistance can be precisely tailored to specific industrial applications.
Annealing serves as a fundamental heat treatment for high carbon steel plates, particularly when improved machinability is required. The process involves heating the steel to temperatures between 750°C and 900°C, followed by slow cooling in the furnace. This treatment relieves internal stresses from previous rolling operations while producing a soft, pearlitic microstructure that facilitates subsequent machining or forming operations. Some manufacturers employ isothermal annealing techniques to achieve more uniform hardness across large plate surfaces, especially important for components requiring precise dimensional stability.
Quenching and tempering processes create the optimal balance of hardness and toughness needed for demanding applications. After austenitizing at temperatures typically ranging from 800°C to 850°C, the steel is rapidly quenched in oil or water to form martensite - an extremely hard but brittle microstructure. The subsequent tempering stage at 200°C to 600°C then reduces brittleness while maintaining sufficient hardness. Advanced heat treatment facilities now utilize computerized controls to manage these processes with exceptional precision, ensuring consistent results across entire plate surfaces.